

Locates based on trigger point, rather than release point. Restore EEPROM feature: A new set of restore EEPROM features to help OEMs and users reset their Grbl installation to the build defaults.Valid Non-Command Words: F, I, J, K, L, N, P, R, S, T, X, Y, Z.
#Candle grbl controller return coordinates software
There are several open source software programs that run on your computer and feed G-code files to the Arduino to run a CNC Machine. That means the controller will look up to 18 motions into the future and plan its velocities ahead to deliver smooth acceleration and jerk-free cornering.
#Candle grbl controller return coordinates full
Grbl includes full acceleration management with look ahead. Functions and variables are not currently supported, but may be included in future releases in a form of a pre-processor. Arcs, circles and helical motion are fully supported, as well as, other basic functional g-code commands. It accepts standards-compliant G-code and has been tested with the output of several CAM tools with no problems. It is able to maintain up to 30kHz of stable, jitter free control pulses.
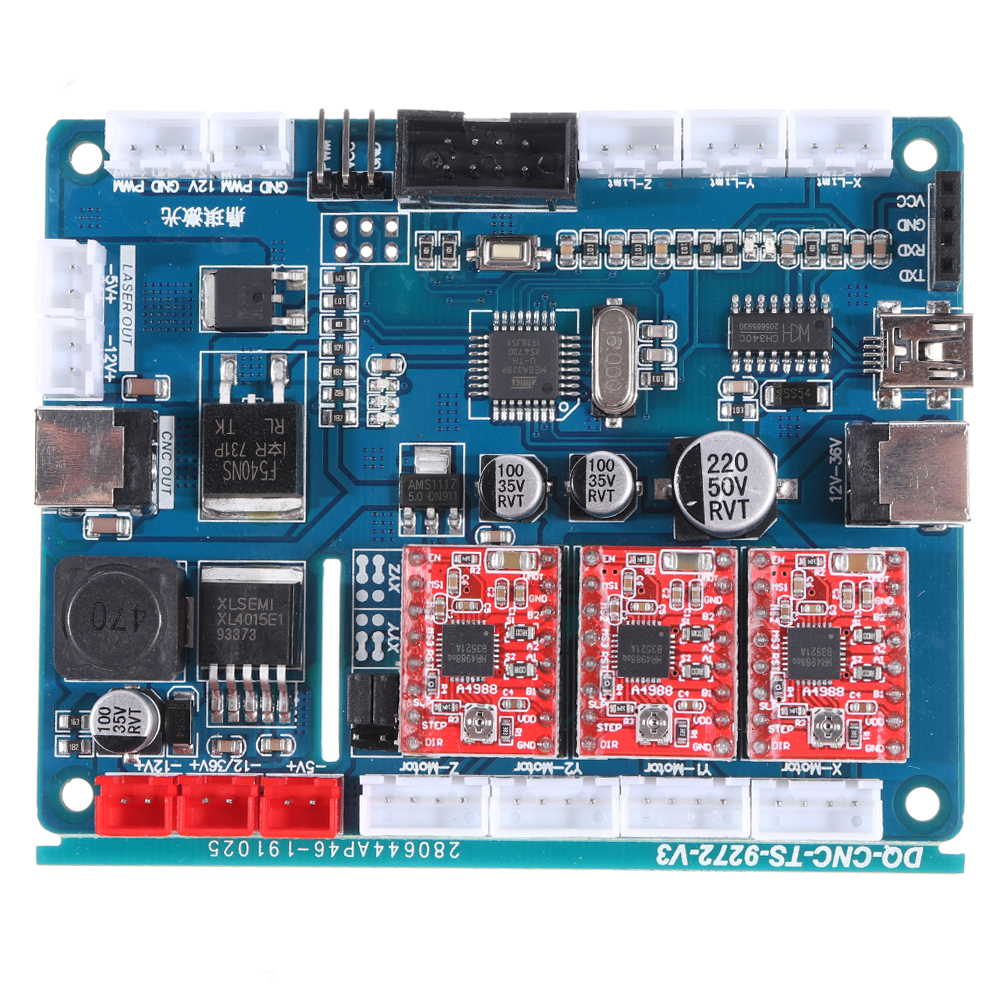
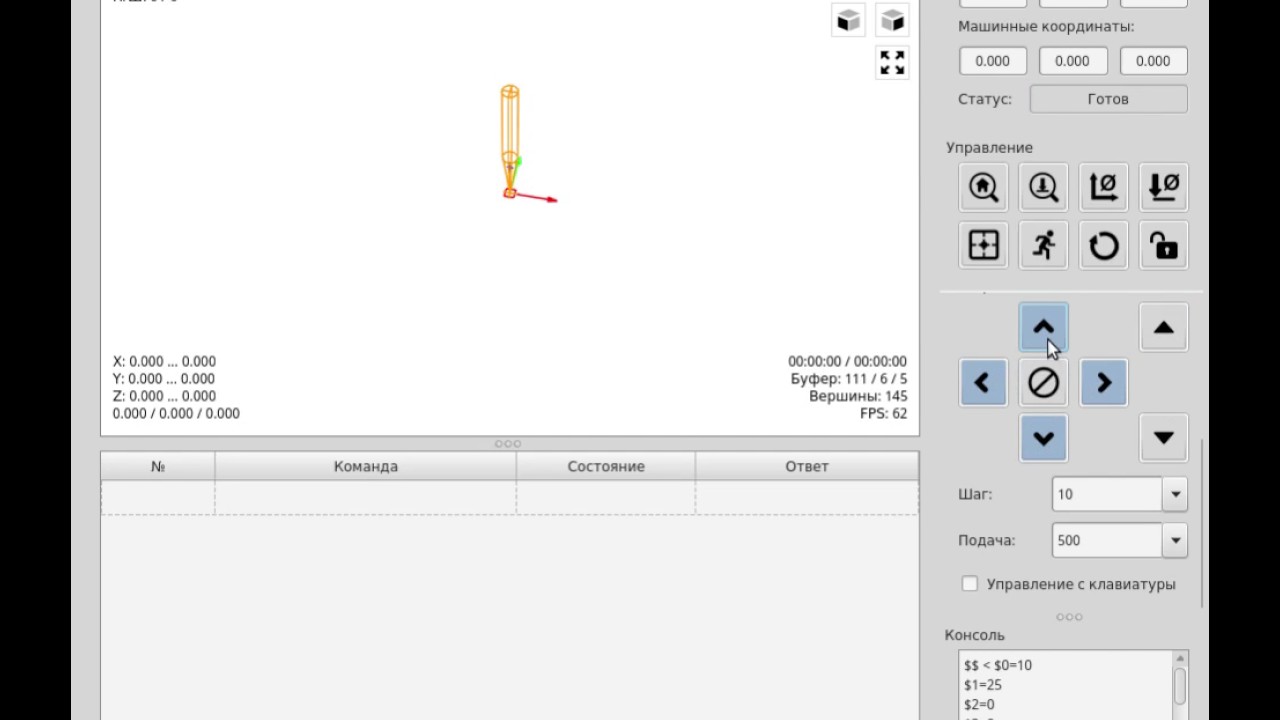
The controller is written in highly optimized C utilizing every clever feature of the AVR-chips to achieve precise timing and asynchronous operation. It will run on a vanilla Arduino (Duemillanove/Uno) as long as it sports an Atmega 328. Grbl is a no-compromise, high performance, low cost alternative to parallel-port-based motion control for CNC milling. Grbl (pronounced gerbil) \ˈjər-bəl\ is a CNC controller software that runs on an Arduino (or similar) microcontroller.
